How do electronics companies ensure their devices can survive a plunge into the ocean or keep working as temperatures drop toward zero? How does a furniture manufacturer determine the limits of its 10-year guarantee? And how can you trust that your phone’s battery won’t overheat when left in the sun?
Rigorous environmental testing is key across industries—whether producing electronics, medical devices, automobiles, or furniture. These tests simulate real-world conditions to identify design weaknesses and establish reliable performance standards, including warranties.
At the core of these evaluations are environmental test chambers. This guide’ll explore everything you need to know—from the different chamber types and how they work to practical use cases and more.
What Are Environmental Test Chambers?
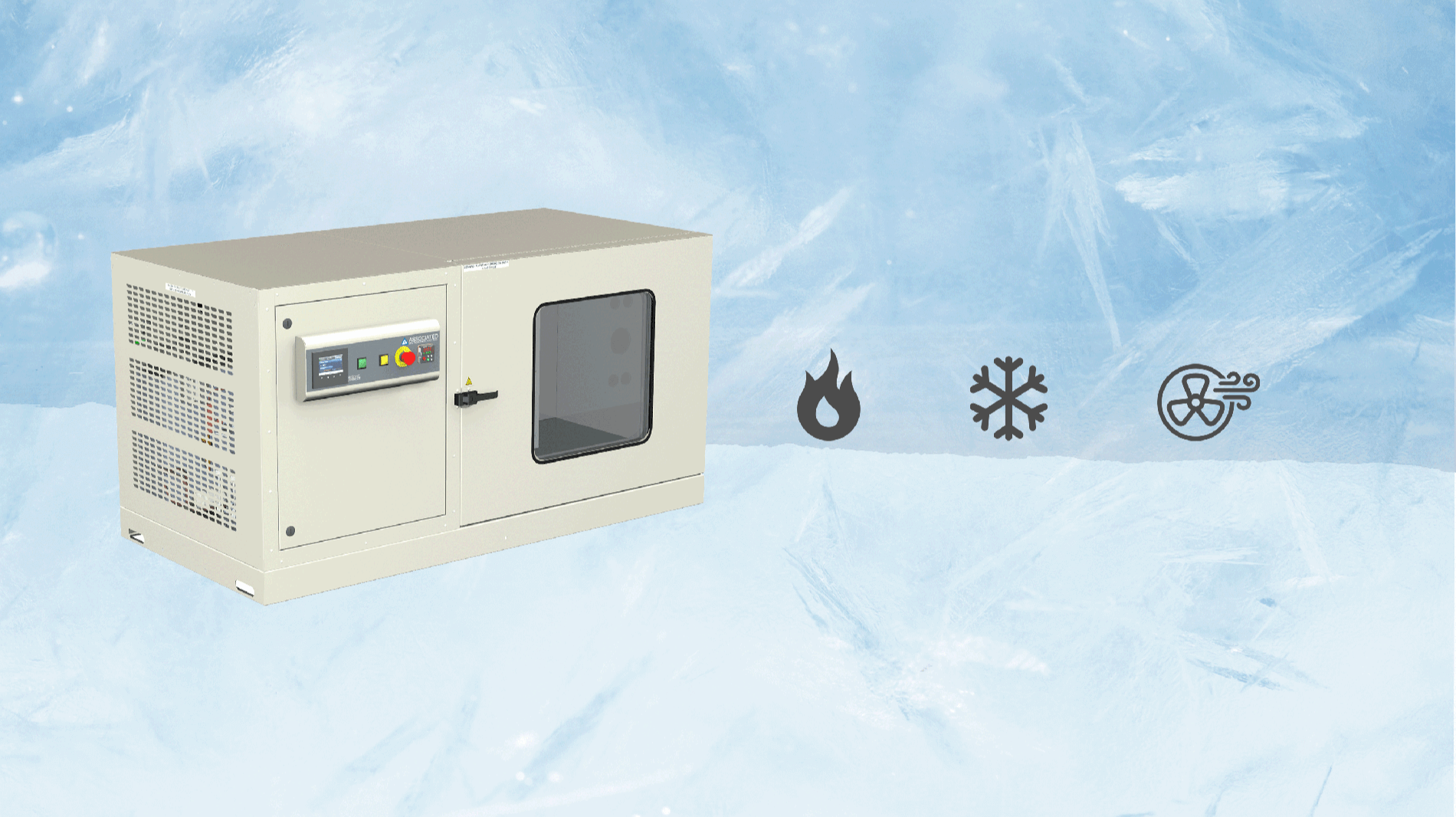
An environmental test chamber, also called an environmental chamber, test chamber, or climatic chamber, is designed to replicate controlled environmental conditions within an enclosed space. These chambers are used to test and evaluate the performance, durability, and safety of products across industries. Engineers, researchers, and manufacturers rely on test chambers to push the boundaries of innovation while ensuring the safety and reliability of their products.
Test chambers come in a wide range of sizes, from compact benchtop models measuring just half a cubic foot to massive drive-in chambers. These chambers can simulate a variety of environmental conditions, including temperature and humidity, temperature-only testing, and corrosive environments through salt spray testing.
If properly maintained, test chambers can remain operational for 10 years or more.
The type of test chamber you need depends on a number of factors, namely the lab space available to you, the products or components you’re testing, and the standards (see Testing Standards section) to which you’re testing. (For more information on how to determine what test chamber to purchase, read our Test Chamber Buyer’s Guide).
Below are common types of test chambers, categorized by physical style and performance.
Test Chamber Styles
Benchtop
Benchtop test chambers range in volume from 1.5 to 8 cubic feet. They’re designed to sit on workbenches so the test chamber operators can easily place and remove the devices they’re testing. Benchtop models are primarily temperature and humidity chambers, ideal for steady-state or temperature cycling testing.
Floor
Floor models are set directly on a lab’s floor. They can range in size from 1.5 to 264 cubic feet or more of volume.
Rack and Stack
Smaller test chambers can be stacked on top of each other without sacrificing performance. They’re popular size options for companies who own multiple test chambers and limited lab space. With stackable models, you can also run independent tests concurrently. Some of our models can even be racked and stacked three chambers high.
Walk-In & Drive-In
As the names suggest, these test chambers (either built with panels or as one structure) are big enough for engineers to walk in, either to test large (perhaps oddly shaped) products or a large number of products at once. Drive-in test chambers enable engineers to test all sorts of vehicles and even smaller aircraft.
Test Chambers
Temperature Only
Temperature-only test chambers allow users to conduct steady-state tests or temperature cycling. They also can feature radio frequency shielding, a crucial component for companies in the electronics industry.
Temperature and Humidity
Controlling the temperature and humidity of a test chamber enables users to recreate real-world, extreme conditions their products might encounter—a cell phone, for example, needs to operate the same way in the freezing cold as it does along the coast in the muggy heat.
Salt Spray
These chambers allow users to test how quickly their products resist corrosion. AES offers transparent salt spray chambers, allowing engineers to observe their products clearly while the test is ongoing.
Thermal Shock
Thermal shock test chambers feature two or three separate zones, with two operating at opposite, extreme temperatures. Devices under test (DUT) are quickly transferred between them, and the third zone adds ambient temperature exposure.
Battery Test Chambers
Battery test chambers simulate real-world conditions your cells will likely encounter, including extreme temperatures and humidity.
AES battery test chambers are safe up to EUCAR level 7.
Laboratory & Liquid Cooled Ovens
Laboratory ovens, ranging in volume from less than a cubic foot to more than 60 cubic feet, are ideal for creating highly stable, controlled, hot air circulation. They’re capable of reaching temperatures greater than 200°C, and are often used for aging, baking, curing, drying, sterilizing, and more.
Liquid-cooled ovens can bring hot ovens down to ambient conditions and as low as -73°C (-100°F) with much faster pull-down rates than traditional test chamber mechanical refrigeration. With LN2 or CO2 boosts, liquid cooled ovens can reach cryogenic levels, as low as -185°C.
Specialty Chambers
A selection of chambers fall outside traditional performance requirements. AES’s HM-436 model is a steady-state test chamber designed specifically for hydrogen maser atomic clocks. Portable conditioning modules (PCM) enable users to condition the air in the workspace. AGREE chambers have space allocated to add vibration test systems. There are more specialty chambers you may require based on industry, standards you’re testing to, and the devices you’re testing.
Custom-Built Test Chambers
Each manufacturer’s needs are different from the next. That’s why AES is proud to offer fully customizable environmental test chambers made to meet your requirements.
You’ll work with a dedicated sales manager and AES engineers that love to take on new challenges. AES engineers regularly modify existing standard test chambers with custom options specified and configured by your ideas or can design utterly custom test chambers to fit perfectly within your test parameters.
How Do Test Chambers Work?
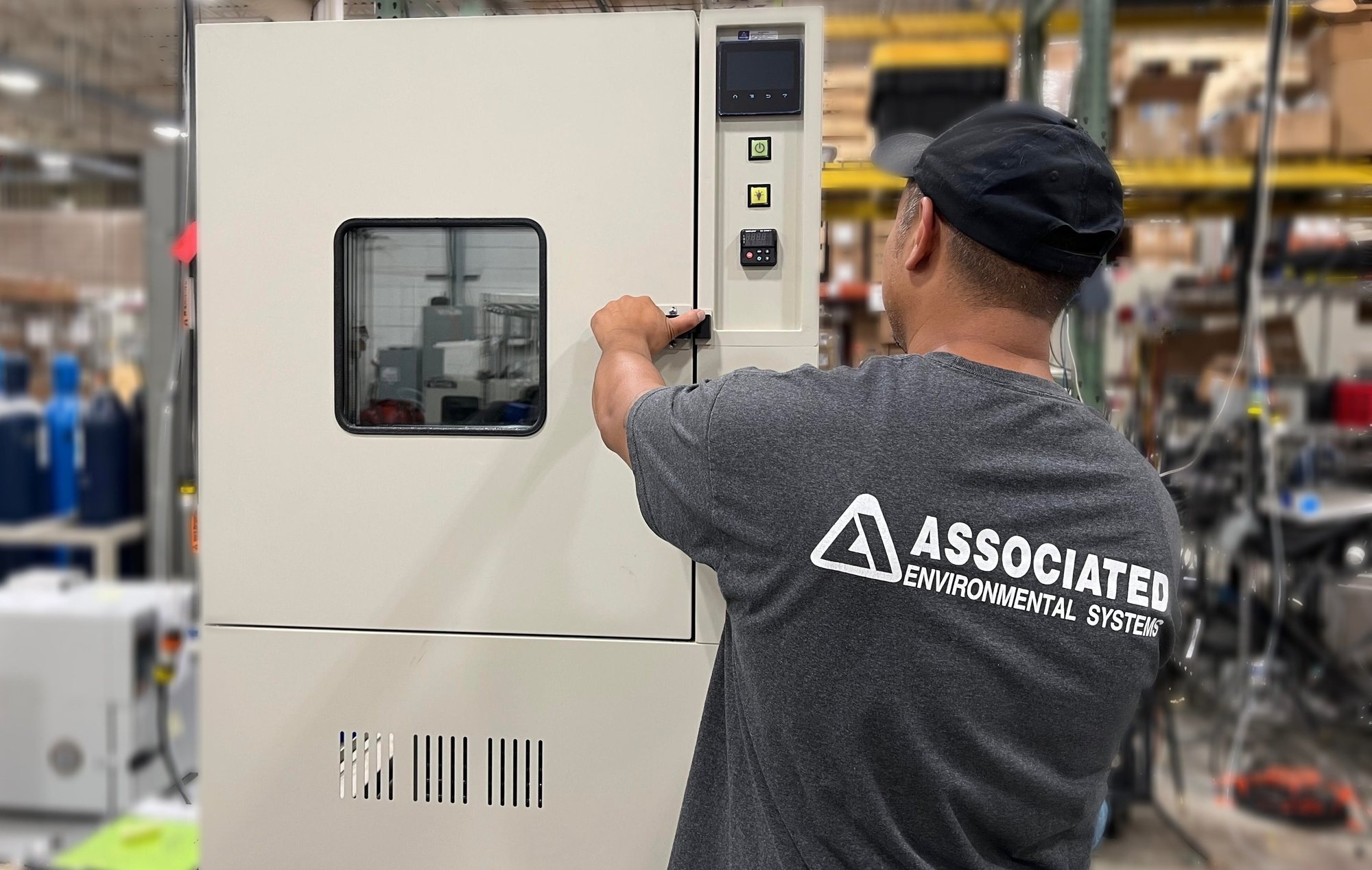
Depending on their purpose, test chambers have different systems that go into creating and maintaining the environmental conditions. We’ll briefly go over air circulation, cooling, heating, humidity, and salt spray since they’re common.
It’s important to learn and understand the specifications of your particular test chamber and to keep the manufacturer in close contact. If you’re in need of service, know that AES repairs, maintains, and troubleshoots all test chambers, regardless of manufacturer.
Air Circulation
Air circulation is crucial for environmental testing as the conditions in the lab and inside the test chamber both factor in delivering accurate results. AES’s test chambers feature a baffle and fan combination to optimize temperature and humidity conditions within the workspace.
Cooling & Refrigeration
Test chambers can reach extremely low temperatures (think -70 degrees Celsius) and quickly: The refrigeration systems on AES chambers have various pulldown rates, averaging between 2.5 and 10 degrees Celsius per minute. It’s a compact, sealed mechanical system for easy maintenance. When supplemented with boost cooling in the form of liquid carbon dioxide or liquid nitrogen temperatures can fall even lower and faster which may be necessary for rapid cooling during stress tests.
Heating
Modern test chambers feature electric heating systems where air passes over independent, fast-response nichrome heaters with ceramic cores to deliver accurate, controllable results. Standard models can reach temperatures 120 degrees Celsius and well above, with precision to within +/-0.5 degrees.
With heating and cooling, it’s important to keep in mind that the intended performance level of your test chambers. Although standard models can reach high and low temperatures, they may not be able to maintain temperature extremes or change rates without compromising the smaller compressors. Always consider the heat absorption rate of your product being tested as that will also affect performance expectations.
Humidity
To create humidity, vapor steam generators are custom-fit and attached to test chambers. They rely on a properly conditioned water source to produce humidity ranges from 20 to 95% relative humidity (RH). With special devices humidity can be controlled within 10 to 98% RH. To remove unwanted humidity, a mechanical dehumidifying system is often used to speed up the pulldown process. Some test chambers are made to keep humidity tightly controlled when temperature is going up or down. Users who need to reach humidity levels as low as 5% RH add desiccant air dryers to their test chambers.
Salt Spray
To create the salt spray, a salt solution is prepared and stored in a tank, then compressed air is used to force the solution and conditioned water through a nozzle and create a fine mist in the test chamber. AES’s MX Series chambers are a unique style of salt spray chamber. Its clear walls allow for total product visibility during testing.
Test Chamber Use Cases
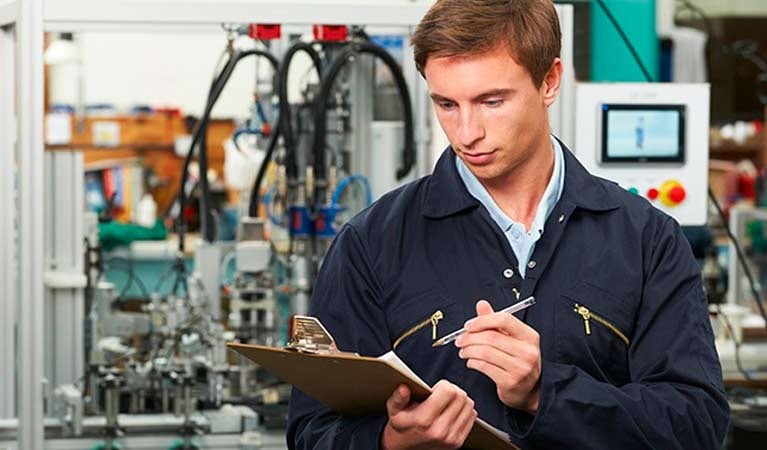
Companies conduct environmental testing at various phases of product development. For newer companies, it’s crucial for prototyping and proof of concept. For established companies, testing confirms innovations and helps them reach the market faster.
Research & Development (R&D)
R&D testing is essential to identify potential weak points early, preventing costly issues later. Environmental chambers simulate real-world conditions like temperature shifts and humidity to evaluate product durability through highly accelerated life testing (HALT). The insights gained guide decisions for further design or material improvements.
Prototyping & Proof of Concept
Before production, companies validate designs by testing performance under different environmental conditions. This ensures that the product meets the required standards before moving forward with full-scale manufacturing.
Production Testing
Production testing ensures product reliability by using techniques like highly accelerated stress screening (HASS). Some industries, like medical devices, test every unit, while others rely on batch testing. This phase verifies that products meet quality standards before reaching consumers.
Quality & Reliability Testing
Quality assurance (QA) and control (QC) testing ensures products meet industry or regulatory standards. Reliability tests subject products to extreme conditions to confirm they can withstand stressors identified in HALT, reducing the risk of failure after release.
Safety & Compliance
Certain industries require safety and compliance testing to meet regulatory standards. Environmental chambers assess how products perform in hazardous conditions, ensuring they meet the safety requirements necessary for market approval.
Testing Standards
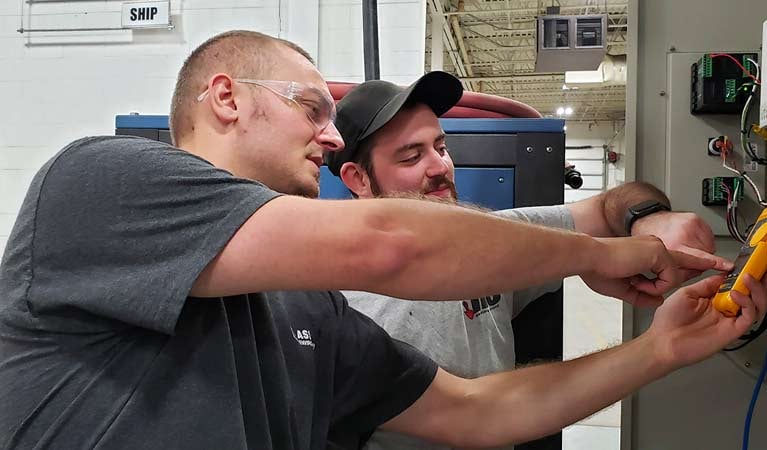
Environmental test standards establish criteria for a product’s, material’s, or component’s ability to withstand different environmental conditions for a period of time or over a projected lifetime.
Standards vary according to the industry, the type of item being tested, and its intended use. Examples of environmental or climatic conditions to which standard testing parameters apply include:
- Extremely high and low temperatures
- Rapid variations in temperature
- Humidity variations
- Salt spray and salt fog
- Vibrations
- High and low pressures
Environmental test standards apply to a wide variety of industry sectors, and some standards apply to more than one industry. These are some examples of specifications organized in alphabetical order:
Request More Info
Associated Environmental Systems has customized test chambers for companies in many different industries. We're ready to answer your questions. Please call us at 978-486-5079 or send us a message.