What Are Amperage Hours & Why Are They Important?
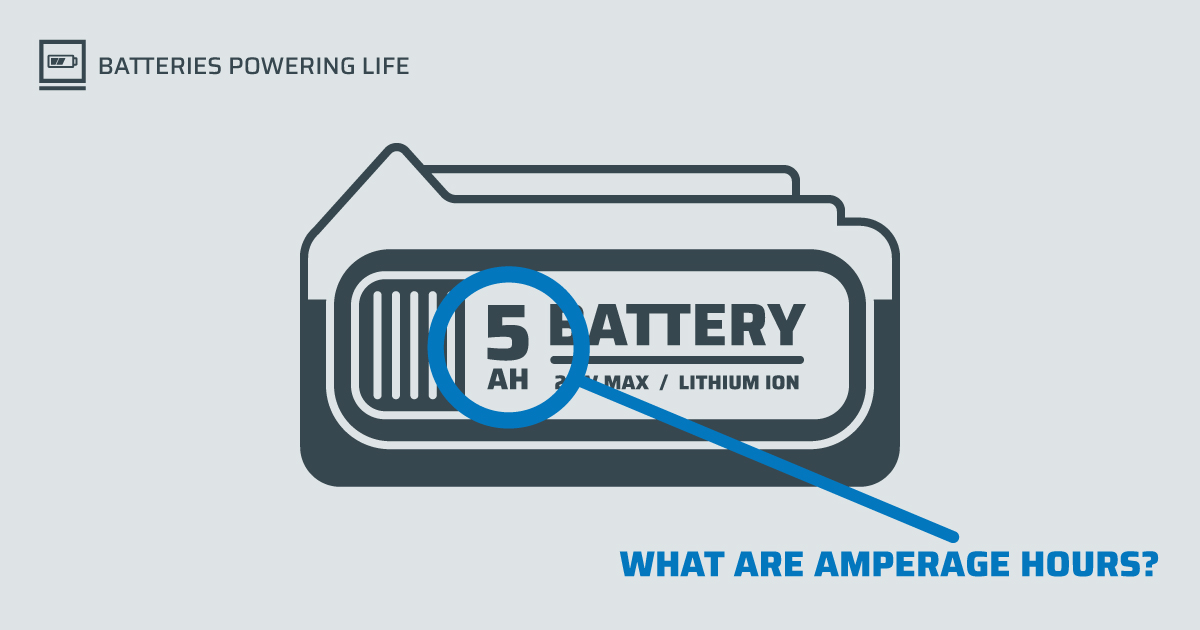
The importance of reliable power cannot be overstated, as batteries continue to advance and are present in our everyday lives. Understanding amp hours is essential to further research and development of today’s most important technologies, particularly for safe and efficient battery testing.
Let’s look at amp hours and what they mean for battery testing.
What Are Amp Hours?
Amperage hours is a measurement of electric charge, identifying how long a battery can provide one ampere of power per hour. Put another way, it’s the amount of energy that facilitates one ampere of current flow through a conductor for an hour.
While watts (wh) refer to the energy storage capacity of a battery, and voltage measures the electrical power of a device, amp hours relate to the electrical charge within the battery. Amp hours are abbreviated as Ah or mAh for milli-amp hours (common to smaller battery applications).
Battery Storage Capacity Formula
You can determine battery storage capacity with a simple formula:
Energy stored in a battery (E) equals battery voltage (V) multiplied by the battery’s electrical charge (Q), or E = V x Q.
And in order to calculate the amp hours, you plug in voltage (V) and energy stored in watts (E) in the battery storage capacity formula. For instance, if your 9 volt battery puts out 5 watts of energy, then 5wh = 9V x Q.
So, Q = 5wh / 9v.
That gives you .56 ah for your electrical charge.
Amperage Hours & Battery Testing
Batteries, specifically lithium-ion ones, power our modern world. Think about the number of handheld devices, alone, you interact with every day. In fact, we touch our smartphones an average of 2,617 times a day, according to research firm Dscout. They’re also utilized in medical equipment, mass telecommunication, electric vehicles, laptops, and aviation.
Without testing batteries to ensure these devices function safely and reliably, many technological advancements wouldn’t be available to consumers today. It takes hours and hours of research and development to guarantee devices under testing (DUTs) are ready to go to market. Engineers want to be confident their batteries (and devices) perform to consumer expectations.
So what goes into battery testing?
Lithium-ion batteries are widely used because they’re lightweight, very reactive with a high-energy density, recharge quickly, and have a slower discharge compared to other chemicals.
One testing method to determine the durability and reliability of batteries involves placing them inside environmental test chambers where a combination of extreme temperatures and humidity is applied to simulate real-world conditions. The environmental test chamber is designed to withstand any explosion or leakage that may occur during a battery event, minimizing any risk associated with testing.
Testing batteries in this controlled environment means they can be charged and discharged safely, which makes rating amperage hours safe and accurate. Amperage ratings for batteries are based on how well batteries perform a variety of tasks under these testing conditions.
Knowledge of amperage hours is necessary because it gives engineers a reliable way to assess their batteries' performance under varied real-world conditions. In the case of EVs, for instance, driving in high altitudes or extreme weather conditions makes extra power demands on batteries. Also, by testing the amperage hour rating of a battery, users will know how much a battery can store, and how long it can deliver, power before recharging.
Ahead of going to market, engineers need to be certain amperage hours remain consistent with the many circumstances they’ll likely encounter: city, highway, mountains, flatland, rainstorms, etc.
Battery Testing & Safety
With all this concentrated power comes some challenges.
Batteries are inherently dangerous due to the possibility of a thermal runaway. This occurs when more heat is generated than can be dissipated, and it is a rare occurrence. If battery cells are positioned too closely together, a chain reaction can occur, causing thermal runaway to propagate from cell to cell. This can create more heat, leading to fires, explosions, and damage to equipment.
Thermal runaway events are also dangerous when testing large quantities of batteries at the same time or screening high-capacity batteries, because the pressure generated creates a lot of force. However, testing in a controlled environment with battery fixtures and battery testing chambers with built-in safety features dramatically reduces potential dangers.
It is also important to factor in the total energy density in a chamber. Reliable manufacturers identify the total energy in the chamber and design it to safely test battery cells, especially when a thermal runaway is possible. They will size the pressure relief to handle the amount of gas that is generated while minimizing the force that pushes on the chamber door and walls. Chamber manufacturers mitigate circumstances that can lead to thermal runaway by catching pre-thermal runaway events such as cell venting, abnormal cell temperature conditions, electrolyte loss, and voltage/current anomalies.
Given the risks of thermal runaway events, labs will often opt for small-batch testing rather than big-batch testing. Instead of testing a large number of batteries at the same time in an expansive chamber, batteries are distributed throughout multiple smaller chambers, such as stacked benchtops.
This way, if a thermal runaway event does occur, fewer cells will be affected, diminishing the risks that come with accumulated force from explosion or fires. Plus, small-batch testing diminishes the losses from damaged products or damaged equipment. This is why it is extremely important to have cells well organized in a chamber and not have them too close together. By opting for two smaller chambers rather than one larger one, you can spread the cells evenly across the two chambers still within the same footprint. This maximizes not only efficient test results but also safety.
In addition to safety concerns, amperage hours are also important in battery testing because chambers must be capable of accommodating the power generated and conducted by high-density batteries (common to the newest electric vehicles).
Fortunately, Associated Environmental Systems (AES) continues to advance battery testing applications specifically to meet the growing demand for faster-charging and lighter-weight batteries.
High-Amperage Testing Solutions
Specialists in battery testing, AES offers multiple high-amperage testing solutions suitable for nearly every commercial industry, including battery fixtures and battery testing specific chambers. Notably, AES is the only test chamber manufacturer that offers an all-in-one battery fixture and chamber solution.
ATPHEAVY
Built precisely for high-amperage testing, ATPHEAVY can accommodate up to 1000-amp batteries. Also suitable for large prismatic pouch cells, ATPHEAVY fits easily into most temperature and humidity test chambers.
For labs pursuing small-batch testing, this fixture can also be effectively employed in stackable countertop chambers, such as the powerful Super 508.
ATPHEAVY ADAPTABLE
Building upon the success of its predecessor, ATPHEAVY ADAPTABLE is a high-amperage battery fixture with easy-to-adjust components that enable you to accommodate an even wider variety of battery setups and formats. These sliding shelves facilitate users changing batteries outside the chamber, reducing the safety risks of reaching in the chamber.
SC-512-SAFE
More and more EV battery designs are shifting from cylindrical cells to large pouch and prismatic formats. To address this trend, the SC-512-SAFE was created to specifically test larger and higher-density format batteries, becoming even more effective when coupled with the agility of ATPHEAVY ADAPTABLE.
AES’s battery testing chambers can be optimized with a suite of sophisticated safety features. Here are just a few of them:
- An emergency stop button lets users immediately disrupt test chamber function.
- Set point temperature limit prevents you from mistakenly setting temperatures beyond established testing limits.
- High/low temperature limits give users strict control, ensuring cells remain at safe settings.
- Audible and visual alarm sounds, ensuring nothing goes unnoticed when the chamber enters emergency conditions.
- A rapid temperature change feature signals when temperatures shift too dramatically.
- Reinforced stainless steel interior door provides durability users need during high-stakes battery testing.
- Temperature-limited sheath heaters constrain the maximum operating temperature of your chamber.
- Derived from graphite, the burst disk has rupture sensors that trigger the alarm system.
- Chambers will only function if the door is closed and locked.
- Product sensors in the rear of the chamber enable users to monitor DUTs at all times.
- Under an alarm state, a safety feature triggers an inert gas purge.
- If an external terminal block’s voltage signal is disrupted, the chamber alarm input sounds and shuts down the entire system.
- A chamber alarm output disables test equipment for DUTs. Contact closes while the chamber is powered and opens when losing power.
Additionally, ATPHEAVY’s test surface is perforated for optimal airflow. Made of FR4 for heat and fire resistance, which is also non-conductive to prevent accidental shorting of a cell. The IGUS track sits beneath the test surface and neatly organizes all cables and wiring for pulling out shelves with ease.
Ultimately, ampere hours are an important factor in determining the life and energy storage capacity of batteries, and understanding their power is important to researching and developing them safely. With AES’s recent innovations in battery fixtures and chambers, you can be assured that your batteries perform as they should. We set the standards for safe battery testing.
As a leader in designing and manufacturing temperature and humidity test chambers for some of the most innovative products you hold in your hand, drive down the road, and other things we can’t divulge, Associated Environmental Systems gets it. Reach out today to learn more about high-density battery testing.